Manufacturing of facades for kitchen from MDF – secrets of technology
The history of furniture from MDF (from the English MDF – MediumDensityFibreboard) originates in the 60s of the last century, when the USA began to actively use the technology of manufacturing medium-density fibreboard. Although in the furniture production of the post-Soviet countries this material was used only after 30 years, this did not prevent it from quickly gaining popularity and serious competition with particleboard and natural wood. Modern technical means make it possible to manufacture facades from MDF in any form and color palette, but a more important aspect is the unique properties of the material, due to which furniture is able to withstand serious external loads, which is especially important for the kitchen.
Why MDF is the best solution for kitchen furniture
For the production of MDF, various waste from the woodworking industry is used. First they are processed into fine-grained sawdust, which are subsequently compressed under the influence of high temperature. As a binder, a special resin is used that causes minimal formaldehyde emission, which puts this material on a par with the conventional tree in terms of environmental friendliness.
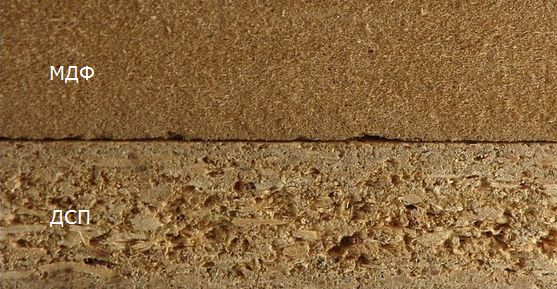
Compared to a chipboard, MDF has a more dense structure
The main advantage of MDF in front of chipboard and natural wood is the lower dependence of the material on the level of humidity in the room. It is known that the chipboard with a short contact with water loses its shape and strength. The tree eventually withers, as a result of which cracks can appear on the furniture, which are not always visible under the varnish, but are perfectly visible under ordinary paint. In turn, a medium density fibreboard is less susceptible to such deformation processes, so it is more often used for the manufacture of kitchen facades.
Note: The ability of MDF to resist moisture is determined by the density index. On average, the density of such material from different manufacturers is 700 kg / m³. If it exceeds 1000 kg / m³, then the cooker is able to safely transfer the high humidity of the air in the room without the additional use of moisture-resistant impregnations.
Despite its strength, MDF refers to soft materials and is very easy to process, so furniture makers and designers like working with it so much. Having a milling machine at hand, it becomes possible to produce almost any profile. If the design of the kitchen assumes the presence of semicircular elements, the press can bend the sheet to the desired shape.
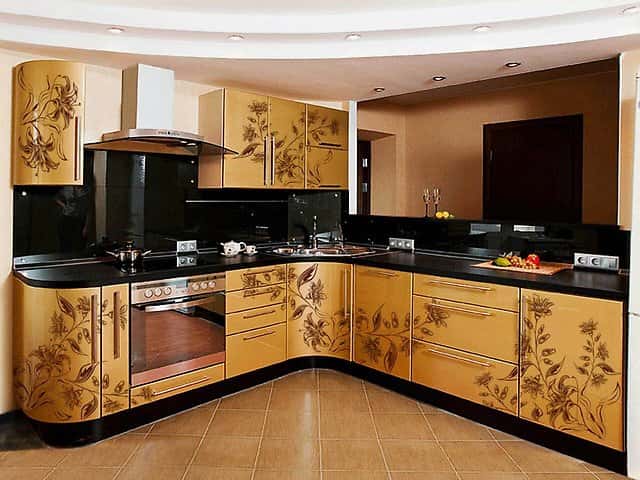
Designer kitchen from MDF
Professional production of kitchen MDF-facades
The process of manufacturing furniture facades with the use of specialized equipment includes several technological stages:
- Cut sheet;
- surface milling;
- exterior finishing.
Cutting sheet material
MDF sheets used in furniture manufacture initially have a large format, therefore they are subjected to additional cutting. Sawing of the material according to the specified dimensions is carried out on format-cutting machines that can cut at any angle. The depth of cut in such machines is 21 cm, allowing you to cut several sheets at once, which is very convenient in case of mass production.
To make a facade of MDF with a uniform coating, it is necessary to completely exclude the presence of micro-chips and other defects that may appear after manual cutting. Modern format saws with special wheels allow you to immediately achieve the ideal result, so the end surface does not require serious processing. Before the edge is pierced, the face of the facade is subjected to only a fine grinding to remove the wood dust after cutting.
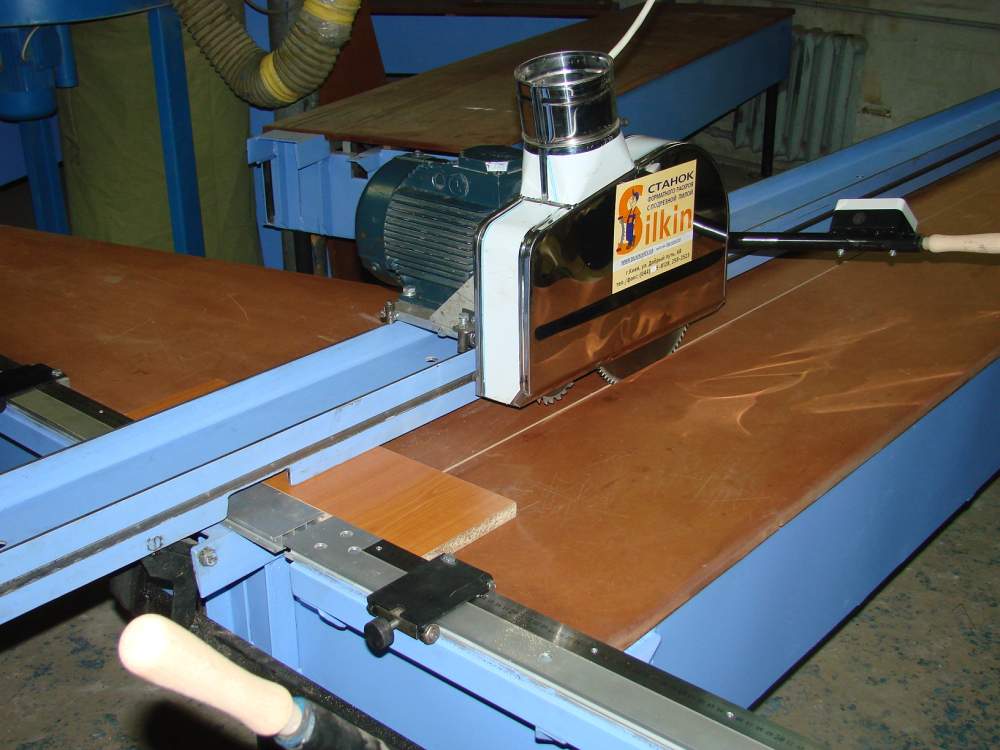
Cutting of sheet material on a format-cutting machine
Surface Milling
If the design of the kitchen assumes the presence of even facades, then there is no need to milling the external plane. However, very often customers require the manufacture of furniture with original decorative elements, for which the surface processing of the cutting tool on milling equipment.
Important! The quality of milling should be very high. Otherwise, after the application of the decorative coating, the probability of manifestation and strengthening of all malfunctioning defects is high.
For the production of decorative facades from MDF, as a rule, special patterns are used, according to which the cutter cuts out the necessary contour on the surface of the plate. At advanced enterprises for such purposes, CNC machines are used, which allow creating absolutely any drawing in a few minutes.
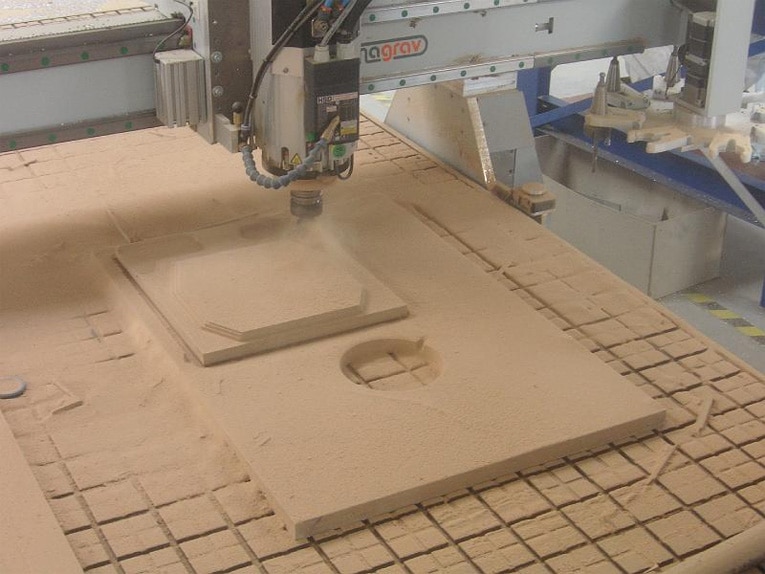
Milling on MDF with CNC
External finish with polymer film
Finishing of facades is an important stage in the production of kitchen furniture, since the life of the product largely depends on the quality of the external coating. MDF can be coated with enamel or polymer film. If the painting of the facade is quite feasible at home (this technology will be discussed below), the lining of the prepared part with PVC film is only available in the shop with special equipment – thermovacuum press.
The facade is decorated with a polymer film in the following sequence:
- The ends and the outer plane of the part are covered with a layer of glue.
- The facades are evenly laid out on the thermovacuum press table.
- A polymer film of suitable color is placed on top.
- On the table, the protective casing, which isolates the parts and the film from the external environment, is lowered.
- Turns on the heating of the working space with simultaneous evacuation of air to create the necessary vacuum.
- Under the influence of high temperature and negative pressure, the film softens and tightly envelops every detail.
- At the end of the cycle, the parts are cooled, after which an excess film is cut along the contour.

Manufacturing of facades from MDF on thermovacuum press
How to make facades for the kitchen at home
If there is a desire and technical possibilities, it is possible to make kitchen MDF-facades independently. This will require:
- a plate of MDF;
- Circular Saw;
- sandpaper of different granularity (P180-240, P320-400);
- Scotch-Bright;
- wood filler for wood;
- soil-insulator;
- polyurethane primer;
- acrylic enamel;
- acrylic lacquer.
Sawing MDF plates
To make facades for the kitchen, first you need to buy a plate of MDF. Usually, the furniture makers use sheets 16 mm or 19 mm thick – this is enough to create reliable kitchen furniture. Of course, you can buy a sheet of a larger size, but this does not make much sense, unless such thickness is needed to implement some design idea.
By purchasing MDF from furniture makers, you can cut it immediately, taking into account the required dimensions. The average price of such a service is 40-50 rubles. per meter of cutting. If you have every kopeck on your account, you can do this job yourself, for which you need a circular saw.
Advice! Professionals recommend using a carbide saw with fine teeth for cutting MDF sheets. This will avoid the occurrence of serious cutting defects.
To simplify the work, it is better to pre-divide the slab into several smaller fragments, then cut out the details for future kitchen facades. Despite the fact that MDF is less prone to fracture than chipboard, it is necessary to be very careful in cutting to avoid micro-chips or at least reduce their availability to a minimum.
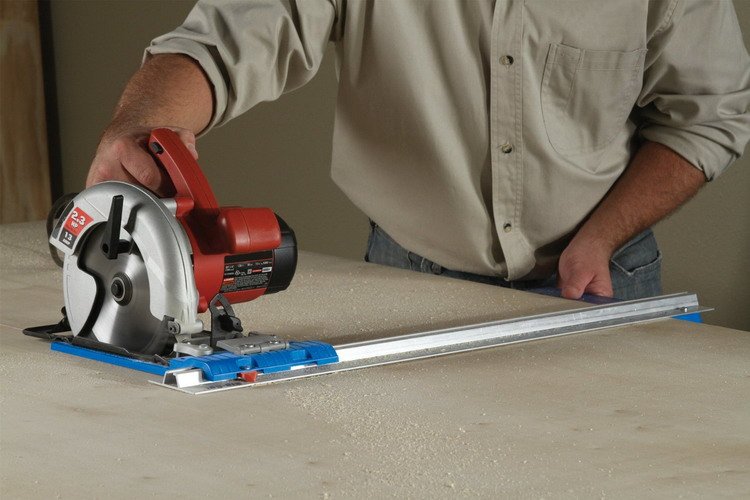
To make kitchen facades without curvatures, the saw must move using a guiding structure
Surface painting
Film lining, which is performed in the factory, is considered by many to be more resistant to mechanical damage and aggressive cleaning agents. In fact, modern paintwork is also able to withstand the severe loads characteristic of the kitchen, and do not lose their properties over time.
In order for the coating to have a uniform structure and to hold onto the MDF reliably, paint it in accordance with the following instructions:
- Treat the surface of the part with P180-240 emery to remove gloss and create the necessary abrasive.
- Apply filler and allow it to dry (drying – 4 hours).
- Sand the surface with emery P
- Apply soil-insulator (consumption – 90 gr / m², drying – 6 hours).
- Remove abrasive by emery P320-400.
- Apply polyurethane primer (consumption – 150 gr / m², drying – 10 hours).
- Prepare the surface for painting using emery P 320-400 and scotch-brite.
- Apply acrylic enamel (consumption – 200 g / m², drying – 10 hours).
- Open the facade with acrylic lacquer (consumption – 150 g / m², drying – 6 hours).
Advice! Apply primers and paint and varnish materials best using an atomizer or use for this purpose special containers with sprayers.
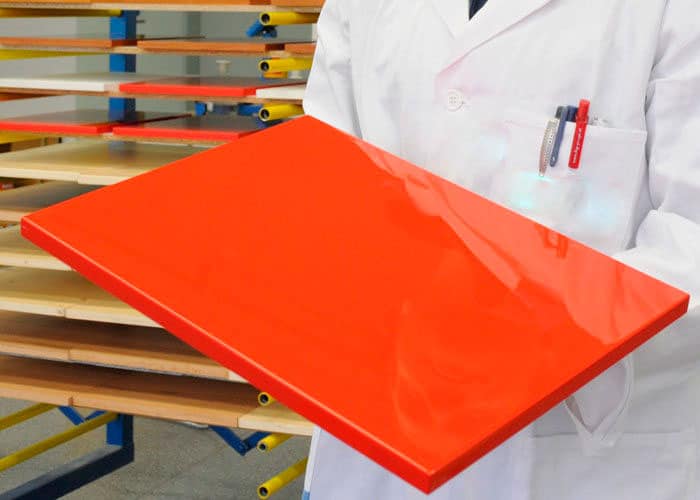
The production of painted facades for the kitchen from MDF must be carried out in a clean and dust-free room
Technology of manufacturing curved facades with your own hands
Sometimes the design of the kitchen involves the manufacture of curved structures that are made in the furniture enterprises with the help of a molding press. To make a curved facade of MDF by oneself, the following technology should be applied:
- Take MDF sheet 9 mm thick and cut out of it two blanks – one for the outside of the facade, the other for the inner. Since the outside radius is larger, the outer part should be slightly longer.
- Make a template for forming a semi-circular facade. Any design with a suitable bend radius can be used for this purpose.
- Apply the marking from the inside of the blanks for the cuts, which will allow the sheet to bend. Cuttings must be done only at the point of bending, the distance between them is 5 mm. The saw blade should be adjusted so that the cutting depth is 7-8 mm.
- From a mixture of sawdust and joinery paste, make a paste of medium consistency to fill the incisions. Rub the paste with a spatula, moving it along the cut from the center to the edge to eliminate air pockets.
- After filling the paste with all the cuts, set the inner blank to the template.
- Top to place the outer element of the structure. Between them, the workpieces are fastened with small studs, which can then be easily pulled out. Fix the finished structure to the template with clamps and leave until completely dry.
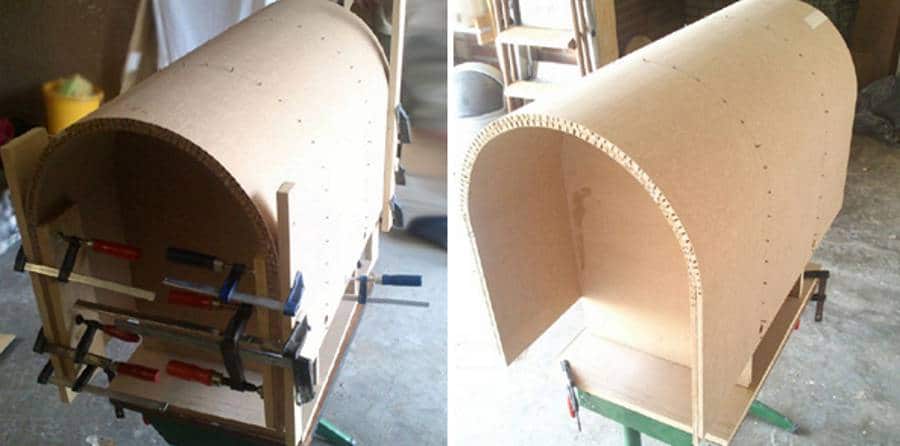
Manufacturing of bent facades
- Remove the dried part from clamps, nails and cut it in accordance with the intended design of the kitchen cupboard.
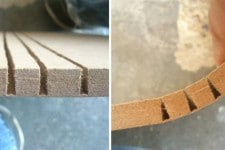
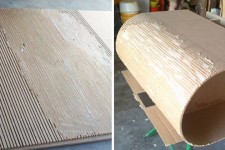
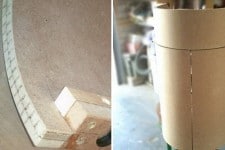
- Prime and paint the product, after which the process of manufacturing the curved facade for the kitchen can be considered complete.
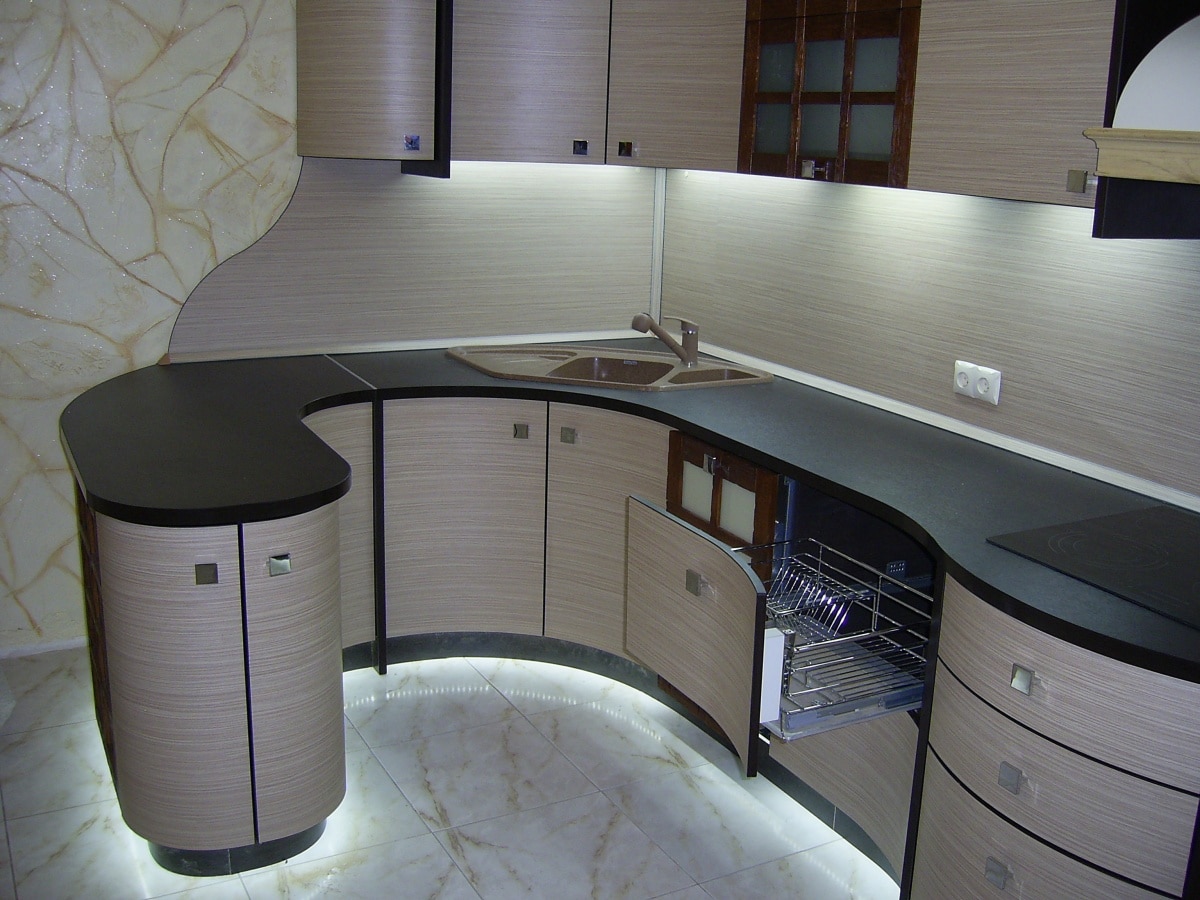
Kitchen bent facades always look stylish and original
Working with MDF is easier than with wood chipboard, because this material does not crumble during cutting and milling. Nevertheless, it is not so easy to make beautiful furniture yourself. Without the relevant skills and experience, it is possible to spoil the product, resulting in the expected savings will turn into a loss. Therefore, the order of kitchen facades from professionals can in the end prove to be more profitable not only in aesthetic, but also in financial terms.